Deciphering the Enigma of Porosity in Welding: Tips for Reducing Issues and Optimizing Quality
In the complex globe of welding, porosity remains a relentless challenge that can significantly impact the quality and integrity of welded joints. As we delve right into the midsts of porosity in welding, uncovering the secrets to its prevention and control will be extremely important for professionals seeking to grasp the art of high-grade weldments.
Recognizing Porosity in Welding
Porosity in welding, a typical concern run into by welders, describes the existence of gas pockets or spaces in the bonded material, which can jeopardize the honesty and high quality of the weld. These gas pockets are normally trapped throughout the welding procedure due to numerous variables such as incorrect securing gas, infected base materials, or inaccurate welding criteria. The formation of porosity can deteriorate the weld, making it at risk to cracking and rust, eventually resulting in structural failures.
By acknowledging the value of preserving appropriate gas protecting, guaranteeing the sanitation of base products, and enhancing welding setups, welders can considerably reduce the chance of porosity formation. In general, a detailed understanding of porosity in welding is essential for welders to produce high-grade and resilient welds.
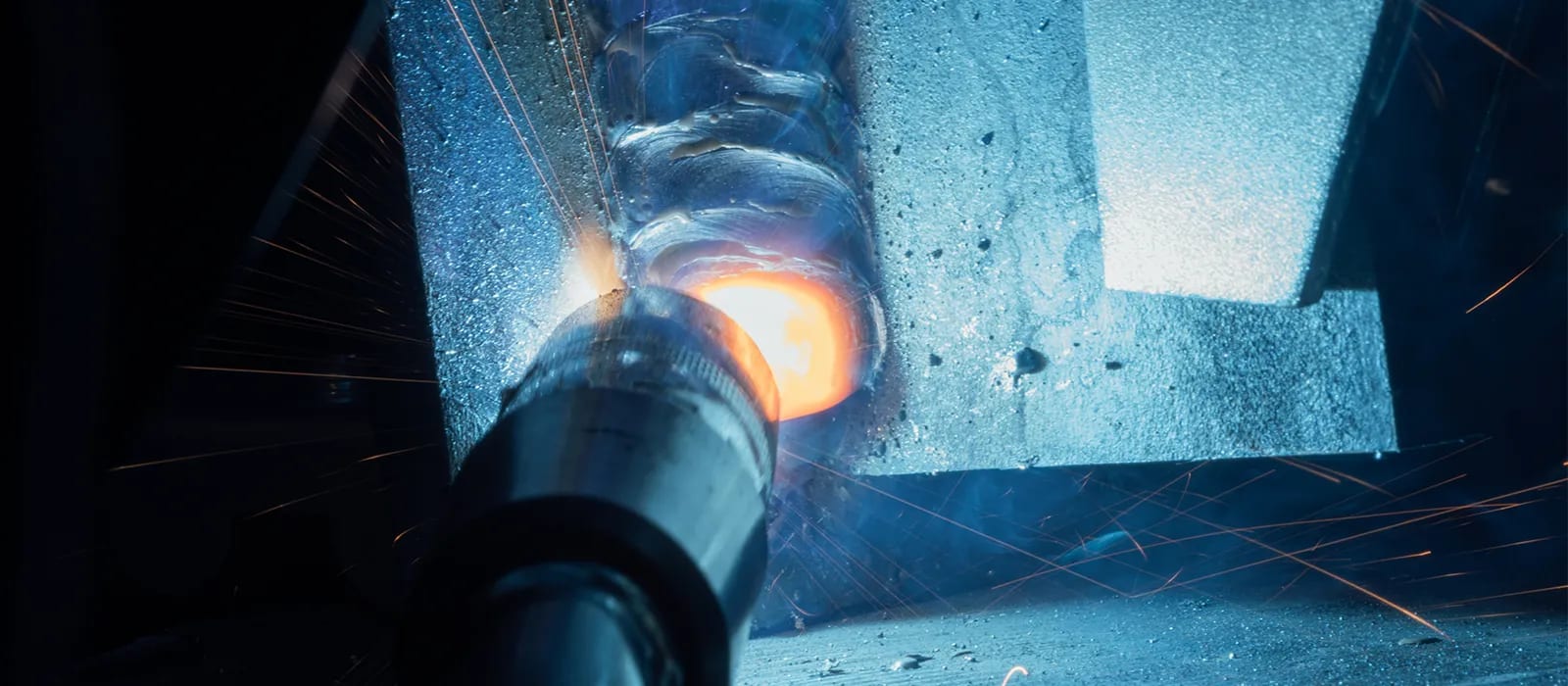
Usual Causes of Porosity
When examining welding processes for possible high quality concerns, recognizing the common reasons of porosity is crucial for maintaining weld stability and avoiding architectural failures. Porosity, defined by the visibility of cavities or gaps in the weld metal, can significantly compromise the mechanical properties of a bonded joint.
Furthermore, welding at improper specifications, such as exceedingly high traveling speeds or currents, can create excessive turbulence in the weld swimming pool, trapping gases and causing porosity. By dealing with these usual causes via proper gas protecting, material preparation, and adherence to ideal welding criteria, welders can decrease porosity and improve the high quality of their welds.
Techniques for Porosity Prevention
Carrying out reliable preventive measures is critical in minimizing the occurrence of porosity in welding processes. One method for porosity prevention is guaranteeing correct cleaning of the base metal before welding. Impurities such as oil, oil, corrosion, and paint can lead to porosity, so complete cleansing utilizing suitable solvents or mechanical techniques is vital.

Another secret safety net is the selection of the right welding consumables. Utilizing high-quality filler materials and shielding gases that appropriate for the base steel and welding procedure can considerably decrease the threat of porosity. Additionally, maintaining appropriate imp source welding specifications, such as voltage, current, take a trip rate, and gas flow price, is important for porosity prevention. Differing the advised settings can result in improper gas coverage and inadequate combination, leading to porosity.
Additionally, using appropriate welding methods, such as preserving a consistent traveling speed, electrode angle, and arc size, can aid protect against porosity (What is Porosity). Ample training of welders to ensure they adhere to finest methods and quality control procedures is additionally vital in decreasing porosity flaws in welding

Finest Practices for Top Quality Welds
Ensuring adherence to sector standards and proper weld joint prep work are fundamental elements of achieving consistently top quality welds. In addition to these fundamental actions, there are numerous best methods that welders can implement to even more boost the high quality of their welds. One secret technique is maintaining appropriate cleanliness in the welding location. Pollutants such as oil, grease, rust, and paint can adversely affect the top quality of the weld, bring about problems. Extensively cleansing the work surface and surrounding area before welding can help mitigate these concerns.
Another finest practice is to very carefully select the suitable welding criteria for the details products being signed up with. Correct parameter option guarantees ideal weld infiltration, combination, and total top quality. Using premium welding consumables, such as electrodes and filler metals, can significantly affect the final weld high quality.
Relevance of Porosity Control
Porosity control plays an important role in this post making certain the integrity and quality of welding joints. Porosity, characterized by the browse around here existence of tooth cavities or gaps within the weld steel, can considerably endanger the mechanical properties and architectural stability of the weld. Too much porosity damages the weld, making it more prone to cracking, deterioration, and total failure under operational loads.
Efficient porosity control is necessary for maintaining the preferred mechanical residential properties, such as stamina, ductility, and toughness, of the bonded joint. What is Porosity. By reducing porosity, welders can boost the total top quality and dependability of the weld, ensuring that it satisfies the efficiency demands of the desired application
Additionally, porosity control is vital for achieving the wanted aesthetic appearance of the weld. Excessive porosity not just compromises the weld however additionally interferes with its visual charm, which can be critical in markets where appearances are essential. Appropriate porosity control techniques, such as utilizing the proper shielding gas, managing the welding criteria, and ensuring appropriate sanitation of the base products, are crucial for producing top quality welds with very little problems.

Conclusion
In final thought, porosity in welding is a typical problem that can compromise the quality of the weld. It is essential to regulate porosity in welding to make sure the stability and strength of the final item.